Being productive is not just about being efficient. Sure, you can tweak a few things here to attempt be more efficient with respect to your numerous renovation, repair, sustainability, and construction projects, but substantial productivity gains require fundamentally changing how you do things.
Doing something more efficiently is not as effective as deploying a process or technique that results in doing something a better way.
Improving construction productivity is not rocket science. The sole reason construction productivity has been abysmal vs. virtually every other business sector is its failure to adopt standardized, proven, and collaborative processes.
Owners must learn more about collaborative and integrated project delivery methods: IPD – integrated project delivery for new construction, JOC – job order contracting or renovation, repair, sustainability, and minor new construction, and PPP – private-public-partnerships.
IPD, and JOC, a form of IPD are neither radical nor new. Both have been around and practiced for decades, however, very few Owners have taken the time to learn about these collaborative methods and/or how to implement them properly.
While “blame” is not the purpose of this article, Owners are, in fact, to blame. They write sign the contracts and write the checks. They have enabled the high level of waste throughout the construction industry.
Improvements of 20-25%+ on the procurement side, virtual elimination of legal disputes, and significant reduction of change orders are just a few of the benefits provided by IPD and JOC. In addition, owners, contractors, and AEs tend to get more work done on-time and on-budget. Also, what is delivered is what was anticipated.
Traditional design-bid-build is not a friend to collaboration and productivity improvement and should be avoided unless absolutely necessary. Low-bid, should most certainly be abandoned unless one is purchasing a commodity and all other variables are consistent.
Poor construction project management and associated traditional construction delivery method lead to unsupportable levels of waste and overall dissatisfaction among all stakeholders – Owners, AEs, Contractors, Subs, Build Product Manufacturers, Oversight Groups, Building Users, and the Community.
Both economic and environmental issues are begin to force change, however, the pace has been glacially slow. Far too much time has been spent upon 3D visualization techniques vs. efficient project delivery methods and associated life-cycle management of built environment.
Collaboration critical, but it’s more than a “buzzword”. Collaboration must be implemented with proven business “best-practices” supported by technology and continuously improved.
The key characteristics of IPD, Job Order Contracting and associated collaborative construction delivery methods are as follows:
1. Early and ongoing joint participation among Owners, Contractors, AEs …
2. Shared risk/reward
3. Transparent and/or standardize costs (example: a unit price book, UPB, based upon RSMeans or other dependable source)
4. Common terms and definitions / ontology
5. Supporting technology with embedded workflows/processes to enable consistent deployment, monitoring, and reduced implementation costs.
Collaborative construction delivery methods such as IPD and JOC change the way most Owners, AEs, and Contractors do things on a day-to-day basis. Long term relationships and transparent information sharing are the norm vs. exception.
Learn more at http://www.4Clicks.com
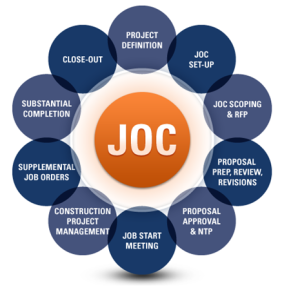