One thing is clear, the construction sector (architecture, engineering, contractors, owners, operators, users, suppliers) has been lagging virtually all other business sectors for decades with respect to productivity improvement.
I believe that the cause is largely cultural, however, any major improvement must be driven by Owners,and/or mandated by governmental regulation.
My reasoning is simple, Owners pay the bills. Thus as long as Owners remain satisfied with the status quo and/or remain “uneducated” with respect to proven business “best practices” and lean management processes, as well as supporting technologies, economic and environmental waste will continue to be rampant.
Currently, my outlook is somewhat pessimistic. If one looks at capability and knowledge specific to life-cycle facility management from an industry perspective, most has originated with the government sector, followed by higher education, state government, healthcare, process-based industries, etc. etc. Basically, Owners whose mission is dependent upon their built environment tend to create and follow life-cycle management practices. These are Owners that can’t adopt a “churn and burn”, or “run to failure” approach to facility management. These sectors can’t easily pack up and move if their facilities and physical infrastructure fail.
That said, even government owners, for the most part, have failed in any sort of department or agency-wide adoption of standardized best practices. This is true even for “simple” areas such as facility repair, maintenance, and renovation. Only the Air Force appears to come close to having any true adoption of robust, proven, best-practices in this regard, as well as associated training, etc., most notably with their SABER construction delivery structure.
In order to effect measurable productivity improvement in the “construction” sector, , I have put together a core requirements “checklist”.
1. Robust Ontology – Cost effective information management and information reuse can only be accomplished with a detailed set of terms, definitions, metrics, etc. This aspect is also critical to improved strategic and tactical decision support mechanisms.
2. An understanding of life-cycle management of the built environment from a collaborative, best-practices, process perspective as well as associated supporting technologies. Forget the traditional strategy-design-construction-demolish approach.
3. Commitment to a total cost of ownership perspective including both economic and environmental costs vs. our classic “first-cost” mentality.
4. “Trust but measure” – Owners MUST conduct their own internal cost estimating and associated capital planning and compare these to contractor estimates, with each party using the same data architecture (examples: RSMeans, masterformat, uniformat, omniclass).
5. Adoption of collaborative construction delivery methods such as Integrated Project Delivery, IPD, and Job Order Contracting, JOC, in lieu of antagonistic and inefficient design-bid-built, or even design-build.
6. STOP reinventing the wheel. Nothing noted here is “rocket science”. Many, if not most, processes, procedures, and technologies are readily available for anyone who does a bit of basic research!!! Also, stop with the focus upon BIM from a 3D visualization perspective! 3D tools are great, and add value, however, INFORMATION and PROCESS drive success.
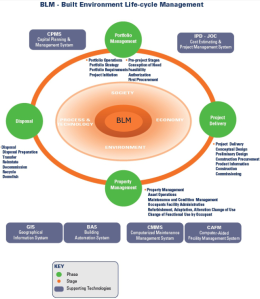